Unlocking Excellence in Injection Molding Tooling: The Role of Superior Metal Fabricators
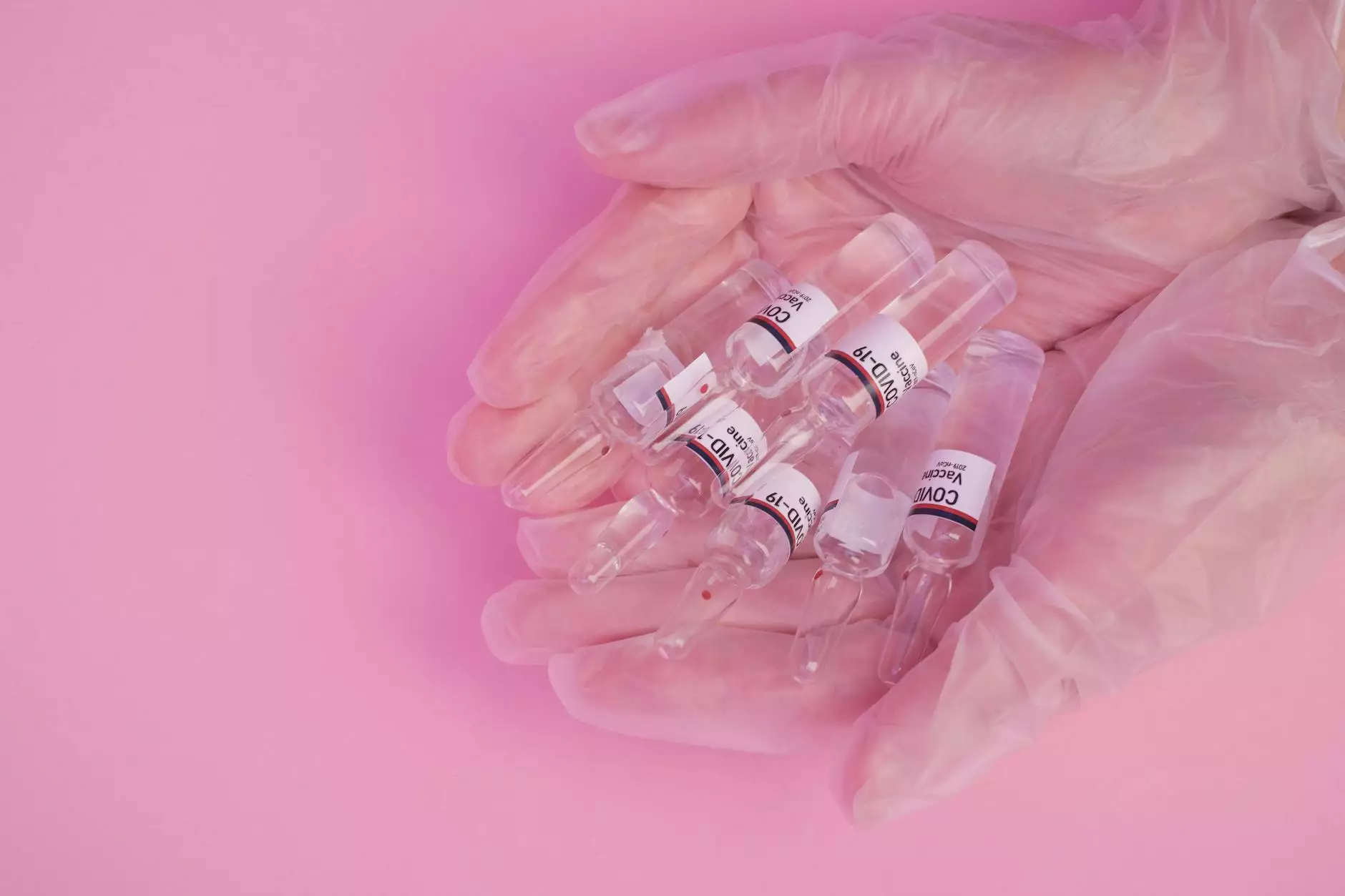
In the competitive world of manufacturing, the significance of high-quality injection molding tooling cannot be overstated. It serves as the backbone for mass production, ensuring that every product meets stringent standards for precision, durability, and efficiency. As a distinguished player among metal fabricators, Deep Mould specializes in delivering cutting-edge injection molding tooling solutions that empower businesses to excel in their manufacturing processes.
What Is Injection Molding Tooling and Why Is It Critical?
Injection molding tooling refers to the meticulously engineered molds used to shape molten materials—most commonly plastics—into specific, complex forms with high precision. These molds are crafted with unmatched accuracy, featuring intricate designs, high-quality steel alloys, and engineered cooling channels to facilitate rapid, efficient cycle times. They are pivotal to production lines because:
- Ensures consistent product quality: Precise molds produce identical items, vital for brand reputation and customer satisfaction.
- Enhances production efficiency: Well-designed tooling reduces cycle times and minimizes waste, leading to cost savings.
- Supports complex geometries: Enables manufacturing of sophisticated and intricate designs impossible through other means.
- Increases mold longevity: Durable tooling withstands heavy usage, reducing downtime and maintenance costs.
Why Choose Deep Mould for Your Injection Molding Tooling Needs?
As an established metal fabricator with extensive experience, Deep Mould excels in delivering tailored injection molding tooling solutions that meet diverse industrial demands. Here are compelling reasons why industry leaders prefer us:
1. Unrivaled Precision Engineering
At Deep Mould, we leverage state-of-the-art CNC machining centers, 3D CAD modeling, and advanced simulation software to design molds with exceptional accuracy. Our experts meticulously analyze each component, ensuring that the final tooling aligns perfectly with your product specifications.
2. Top-Grade Material Selection
We source only premium steel alloys such as P20, H13, S7, and stainless steels, which offer exceptional toughness, wear resistance, and thermal stability. These materials are chosen to optimize mold durability and performance over prolonged production runs.
3. Customization and Flexibility
Deep Mould understands that each project has unique requirements. We offer highly customized injection molding tooling, accommodating complex geometries, multi-cavity molds, and insert molding options to satisfy your specific goals.
4. Quality Control and Testing
Our rigorous quality assurance protocols include detailed inspections, mold flow analysis, and trial runs. We perform trial molding to identify and rectify any issues early, guaranteeing defect-free tooling before delivery.
5. End-to-End Service
From initial design consultation through prototype development, mold fabrication, and post-production support, Deep Mould provides comprehensive services. Our goal is to streamline your entire tooling process, minimizing lead times and maximizing productivity.
The Comprehensive Process of Developing Injection Molding Tooling at Deep Mould
Step 1: Receiving & Analyzing Product Requirements
Our team collaborates with clients to understand detailed product specifications, materials, expected production volume, and tolerances. We gather all necessary data to begin creating an optimal tooling design.
Step 2: Design & Simulation
Using advanced CAD software, engineers craft detailed mold designs. Simulation tools predict how molten materials will flow, cooling patterns, and potential defects, enabling us to optimize the mold for efficiency and quality before manufacturing begins.
Step 3: Material Selection & Fabrication
Based on the design, we select the most suitable steel or alloy. The fabrication process involves CNC machining, electrical discharge machining (EDM), and other precision manufacturing techniques to produce the mold components with tight tolerances.
Step 4: Assembly & Testing
Assembled molds undergo rigorous testing, including trial runs and inspections, to verify performance. Adjustments are made if necessary, ensuring that the final product adheres to strict standards.
Step 5: Delivery & Support
Once approved, the high-quality injection molding tooling is shipped with detailed documentation. We also offer ongoing support, including repairs, maintenance, and upgrades, to extend mold lifespan and maintain output quality.
Advantages of Partnering with Deep Mould for Injection Molding Tooling
- Superior Quality & Durability: Our molds are built to withstand thousands of cycles without degradation, reducing downtime and replacement costs.
- Cost-Effective Solutions: Despite delivering premium quality, our competitive pricing ensures excellent ROI for your projects.
- Fast Turnaround Times: Thanks to our advanced manufacturing facilities and experienced team, we minimize lead times without compromising quality.
- Comprehensive Technical Support: Our experts assist with mold design optimization, troubleshooting, and maintenance, ensuring seamless production processes.
- Environmental Responsibility: We implement eco-friendly manufacturing practices and use sustainable materials where possible, aligning with green manufacturing goals.
Innovation and Future Trends in Injection Molding Tooling
The world of injection molding tooling is continually evolving, driven by technological advancements and increasing market demands. Deep Mould remains at the forefront by embracing:
- Smart Mold Technologies: Integrating sensors and IoT devices for real-time monitoring of mold health, cycle times, and defects.
- Advanced Materials: Developing molds with enhanced thermal management and self-healing properties.
- Rapid Prototyping & 3D Printing: Accelerating the development cycle and enabling rapid iterations.
- Sustainability: Implementing eco-conscious manufacturing processes and recyclable materials to reduce carbon footprint.
Conclusion: Elevate Your Manufacturing with Expert Injection Molding Tooling
In an era where manufacturing precision, efficiency, and sustainability define success, choosing the right metal fabricator for your injection molding tooling is paramount. Deep Mould stands out with its unwavering commitment to excellence, innovation, and customer satisfaction. We empower your business to produce high-quality products with faster turnaround times, lower costs, and superior durability.
Partner with us and experience the difference that expert craftsmanship, advanced technology, and a customer-centric approach can make in your manufacturing journey.
For more information about our injection molding tooling services or to discuss your project needs, please visit deepmould.net.