The Rising Importance of Mould Tool Manufacturers
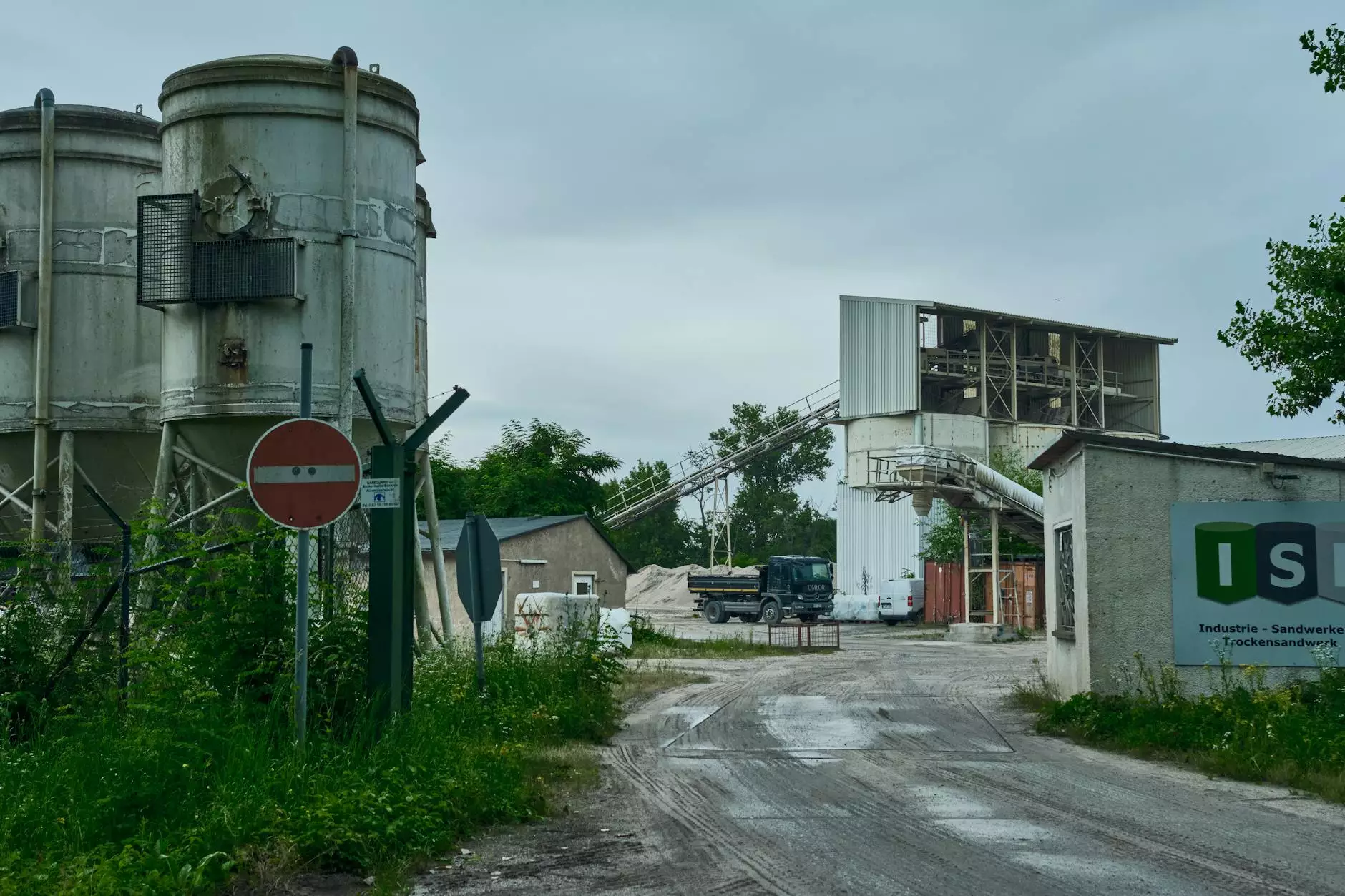
In today's fast-paced industrial landscape, the role of mould tool manufacturers is more crucial than ever. These companies provide the essential tools and equipment necessary for producing a vast array of products, particularly in sectors such as automotive, consumer goods, and medical devices. With the surge in demand for high-quality components, understanding the intricacies of the mould manufacturing process is essential for professionals and enthusiasts alike.
Understanding Mould Tool Manufacturing
The term "mould tool manufacturers" encompasses a variety of processes, technologies, and products, all designed to create quality moulds. These moulds are integral to the plastic injection process, where raw plastic is transformed into finished products. The manufacturing of these moulds involves several key stages:
- Design: This is the initial stage where engineers create detailed specifications for the mould based on product requirements.
- Material Selection: Moulds are typically made from durable materials such as steel or aluminum, chosen for their strength and thermal properties.
- Machining: Advanced CNC machines are used to accurately shape the mould to precise dimensions.
- Assembly: The various components of the mould are assembled to create a functional unit.
- Testing: Before use, moulds are rigorously tested to ensure quality and performance.
The Role of Plastic Mold Makers
Plastic mold makers play a pivotal role in the manufacturing ecosystem, specializing in creating the moulds required for plastic injection. This niche segment of the industry demands high levels of skill and expertise, as the precision of moulds directly influences the quality of the final products. With advancements in technology, plastic mold makers are employing innovative techniques to enhance both efficiency and output. Here’s why they are indispensable:
1. Precision Engineering
The success of any product largely depends on the precision of the mould used to create it. Plastic mould makers utilize advanced CAD software to design complex mould geometries that cater to intricate product designs. This level of detail ensures that products are manufactured with high precision, yielding better fit, finish, and functionality.
2. Cost Efficiency
By producing high-quality moulds, plastic mould makers significantly reduce the need for rework and defects. A well-manufactured mould minimizes material waste and production downtime, leading to lower overall production costs. This economic advantage makes them a preferred partner for many businesses.
3. Customized Solutions
Every product is unique, and so are its moulding requirements. Skilled plastic mould makers can provide customized solutions tailored to specific manufacturing challenges, ensuring that even niche products are produced efficiently.
The Significance of Plastic Injection Mould Manufacturers
Plastic injection mould manufacturers are crucial in the production process, transforming raw plastic material into finished products through a highly mechanized process. This method is prominent due to its ability to produce high volumes of parts within tight tolerances. The significance of these manufacturers can be outlined as follows:
1. Streamlined Manufacturing Processes
Injection moulding is a highly programmable process. Through the use of sophisticated machinery and software, manufacturers can achieve consistent quality across every product line. Optimization of injection moulding not only speeds up production but also enhances product reliability.
2. Diverse Applications
The versatility of plastic injection mould manufacturers allows them to cater to various sectors, including automotive, electronics, and consumer goods. Their ability to produce components of varying complexity enables them to meet the ever-changing demands of the market.
3. Sustainability Initiatives
In an era where sustainability is imperative, numerous plastic injection mould manufacturers are leading efforts to reduce their environmental impact. Through innovations such as developing biodegradable materials and implementing recycling programs, they contribute to a more sustainable future. Companies are now prioritizing eco-friendly practices, making them more appealing to consumers and businesses alike.
Challenges Faced by Mould Tool Manufacturers
Despite the numerous advantages and advancements in technology, mould tool manufacturers still face a variety of challenges. Understanding these challenges is critical for businesses looking to thrive in this competitive landscape:
- Competition: The rapid advancement of technology means more players are entering the mould manufacturing space, increasing competition. To remain relevant, existing companies must innovate continually.
- Supply Chain Issues: Global supply chain disruptions can affect the availability of materials needed for mould production. Manufacturers must develop robust strategies to mitigate these risks.
- Technological Adaptation: Keeping pace with technological advancements often requires significant investment. However, failure to adapt can lead to obsolescence.
- Skilled Workforce Shortage: As manufacturing processes become more sophisticated, the demand for skilled workers is increasing. Finding and retaining qualified personnel is essential for success.
Future Trends in Mould Tool Manufacturing
The future of mould tool manufacturers looks promising, with several trends poised to shape the landscape of the industry:
1. Automation and Industry 4.0
As automation becomes more prevalent, mould manufacturers will increasingly integrate Industry 4.0 practices. This includes the use of IoT devices, data analytics, and AI to optimize production processes and improve decision-making. Such advancements can lead to increased productivity and cost savings.
2. Advanced Materials
The development of new, advanced materials will enable manufacturers to create more durable, lightweight, and heat-resistant moulds. Such innovations will expand the capabilities of plastic injection and enhance performance across various industries.
3. Customization through 3D Printing
3D printing technology is set to revolutionize the way moulds are designed and developed. This technology allows for rapid prototyping and the customization of moulds, enabling manufacturers to react quickly to market demands without incurring substantial costs.
Conclusion
The landscape of mould tool manufacturers is as dynamic as it is essential to modern industries. With a focus on innovation, efficiency, and sustainability, these manufacturers are pivotal in shaping the future of manufacturing. By investing in advanced technologies and maintaining a commitment to quality, businesses involved in mould manufacturing can continue to thrive and evolve in a competitive market like today.
For those looking to partner with industry leaders, companies like Hanking Mould stand out as premier plastic mold makers and plastic injection mould manufacturers. Their commitment to excellence and customer satisfaction ensures that they remain at the forefront of the industry, setting benchmarks in quality and service.